Radically different magnet-free electric motor design represents a major advance in technology
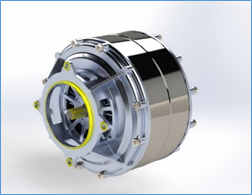
In a world-first, PolyWavePower (PWP) delivers a light-weight magnet-free and highly efficient class of motors in both DC & AC formats using a simplified electronic control driver including low-power static-field control. This new green motor technology can satisfy a very broad range of applications in industry, transportation and renewable energy.
Introduction
Due to global constraints on the supply of strategic rare earth minerals and cost of permanent magnets, many companies today are developing the Switched Reluctance Motor/Generators (SRM) as well as Synchronous Reluctance (SynRM) motor. The rotors of these machines have no magnets or windings, being simpler in construction and easy to keep at lower temperatures as it is not prone to the direct heating that occurs in wound rotors or induction motors.
This trend and the global need for higher efficiency motors and generators is driving many businesses and institutions (including some 65 universities worldwide) to intensify their research in order to compete on the market with this class of machine. However, they are in fact chasing a technology from the 19th century (first patent for this type of machine appears in 1838). The first major advancement in electric motors was the development of solid state electronics in the 1960’s which made possible electronic commutation of the Brushed Motor, again a 19th century invention. The Brushless DC Motor has therefore dominated the EV market until recently when the trend towards SRM motors and generators has grown rapidly using advanced high speed industrial computers to reshape the output/input current of the generator/motor respectively.
It must be pointed out that there has been no new technology in electric machines since the 19th century. Electric rotating machine have improved over time purely due to the advancement of materials and solid state electronics, and lately with modern design methods using computer simulations and optimisation.
PolyWavePower Technology – a genuinely new topology
The new PWP technology patent was filed in January 2021 under International Patent Application with a PCT number available on request. This technology, with its radically innovative topology, offers significant advantages over existing machines. Like the SRM or SynRM machines, there are no magnets or windings on the rotor, however, that is where their similarity ends.
The PWP stator has no ‘slots’ as such*, and PWP electrical machines feature a unique rotor that is ideally shaped in a bi-polar form to exactly respond to the rotating EMF.
*PWP machines are not surface wound but have simple armature coils wound on bobbins. This also applies to the field coils. No specialized winding equipment is therefore required for manufacturing.
Hence it’s near ideal efficiency and the complete absence of cogging. Smooth, ripple free torque is now elegantly achieved for a three phase AC and a DC supplied two phase motor.
Stationary field-pole coils offer complete control over a wide operating range of loads and speeds.
Air or liquid cooling may be applied to the stator; even cryogenic cooling of superconducting field coils is easily achieved due to their external position on the stator. The rotor may or may not have air cooling depending on the application.
Another existing technology in use is the so called homopolar or unipolar alternator or motor. It has many advantages, namely simplicity, reliability and robustness and these machines are therefore used in aerospace, but they suffer from weight and necessarily high operating frequency amongst other deficiencies. PWP electrical machines have bipolar induction and do not suffer from any of the above.
State of the art electrical machines generally have a high number of poles mainly to keep the weight to a reasonably low value particularly in the transport and aerospace industry. PWP machines do not get heavier with fewer poles. The designer has the advantage of combining any number of poles independent of other factors such as diameter, speed, etc. It is therefore possible to have compact machines with 2 or more poles as well as large, ring (annular) type of alternator/motor with 2 or more poles. Its stator ‘back iron’ does not have to be thicker as the number of poles increase, as is the case on classical machines, where the radial flux needs enough stator lamination area to prevent flux saturation between opposite poles.
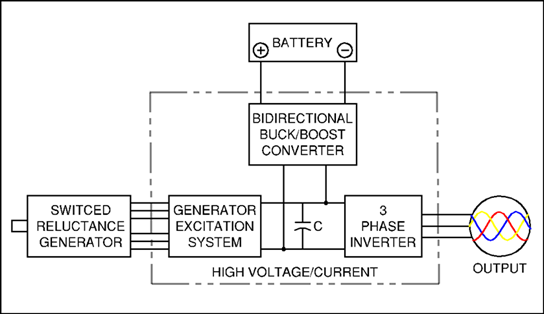
Figure 2: Block Plan for a Switched Reluctance Generator. A SR motor is similar where the 3 phase power is input.
Figure 2 shows power conversion components in a Switched Reluctance Generator. In this type of machine, the power electronics have to process the full current output requiring high current/voltage solid state components adding cost, complexity and reliability issues.
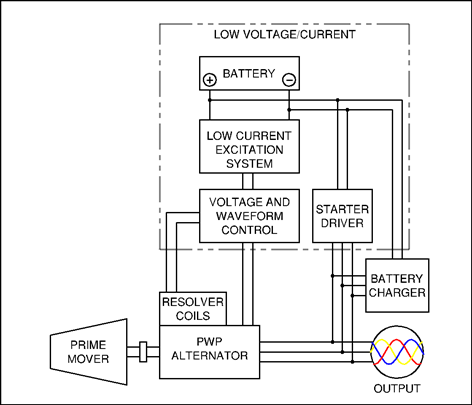
Figure 3 below is a system diagram of a PWP Alternator. Other than the low current excitation system, the output has no electronics. The output is a high quality sinusoidal waveform. A 3 Phase motor would require a standard motor driver modified to include low voltage control of the field coils.
PWP motors may incorporate damper coils which may be sized without space problems, thanks to its unique rotor pole geometry. In this technology the damper coils receive 100% of the flux thanks to the topology.
Therefore, PWP technology is simpler and cheaper then state of the art machines, yet with an efficiency, quality of output current (in the case of an alternator) or torque quality (in the case of a motor) generally on par or surpassing that of state-of-the-art high end machines.
The PWP Motor incorporates simple pick-up coils that generate output signals used to sense rotor speed and position, functioning as a resolver. The stator does not require semiconductor sensors or components. Position and speed may be directly read from standstill to operating speeds with infinite resolution. This is not possible with any other technology unless an expensive resolver is incorporated.
Figure 3: Block Plan for a PWP Alternator that can act as a starter for the Prime Mover (in the case of an ICE or turbine)
PWP Current Alternator for Direct Current Output
All Direct Current supplied PWP motors will use an intermediary wave format being a two phase Alternating Current. This is an ideal current waveform for localised use within a mobile platform as it can be either derived in a very simple way from DC storage, or directly used from a PWP two phase generator without intermediate electronics. This two phase waveform is as efficient as the conventional three phase AC current. Fine control of the alternator or motor output is achieved with considerable flexibility using the low power DC field coil controllers.
BENEFITS FOR COST SENSITIVE MARKETS AND INDUSTRY
PWP motors are able to achieve low manufacturing cost goals through the minimal use of materials, absence of expensive permanent magnets, easy assembly and reduced cost of controllers. However, PWP consumer motors will still benefit from increased reliability and higher maximum power over a wide operating range.
The inherent topological efficiency of PWP industrial motors can be matched to gas or steam turbines or standby ICE plants as well as various Renewable Energy inputs from Concentrated Solar Power, geo-thermal, or steam turbines. All will benefit from very rapid ramp times and ultra-low maintenance.
BENEFITS FOR CARS, TRUCKS AND TRAINS
PWP alternator-motor systems can form a very compact hybrid system with smaller battery packs and low mass on-board generators that make use a zero-carbon fuel for range extension.
As PWP motors do not use permanent magnets, their output can be varied very effectively with only a low power DC field current. A significant operational advantage is possible using magnetic-flux saturation of the rotor for waveform stability and/or short duration power boost. This is not possible with current technology, particularly in the first case, having the opposite effect of distorting the waveform.
PWP open bore Traction motors can be designed around the fixed axle of the locomotive or even the rail-stock. This direct drive avoids the need for a gearbox. Direct control of the whole train can be simplified through the frequency control of the two phase traction current.
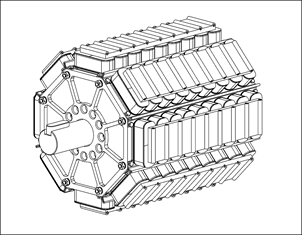
Figure 4: An 8 stage PWP 4-pole 2 Phase motor without casing, showing external armature coils that are easily cooled.
BENEFITS FOR FAN and PUMP MOTORS
PWP motors can optimise their performance under a wide range of speeds using an elegantly simple control of the low power field current. The load efficiency of the motor can be thus maintained at an optimal level. This significantly reduces the cost of controlling large sets of fans.
PWP pump motors can be designed to handle heavy start-up loads without suffering from coil damage. If required, efficient liquid-cooling of the stator coils can be incorporated. Since the rotor magnetism is induced by a DC coil, there is essentially no heating of the rotor poles due to magnetic hysteresis. Very large pump motors can be built with a light-weight rotor, reducing the installation effort.
BENEFITS FOR THE AVIATION AND AEROSPACE MARKET
PWP aviation generators and motors are capable of exceptionally high gravimetric performance due to their simple rotor construction and superior cooling technology. Very high mechanical and electrical reliability can be achieved as PWP technology incorporates comparatively simple motor drivers that further reduces overall mass. A turbine driven two-phase PWP generator can be directly connected to all propulsion motors to meet all flight regime requirements. This is all done by low current field control and in this case, the absence of electronics between motor and generator is particularly significant in terms of safety, redundancy, and reliability.
For PWP Aero-Space generators, the reduced use of electronics adds significantly to overall reliability particularly under arduous radiation exposure experienced in space. PWP has a potentially major future role in a simpler and lighter turbo-pump setup for rockets. A fuel or oxidiser rich turbine can drive a PWP generator which in turn drives separate PWP motors driving fuel and oxidiser pumps. There is no need for expensive seals or inert gas circuits thus completely eliminates any mixing of the fuel and oxidant. Other than low curent field control of the alternator and motors there are no additional electronics. This will improve start-up reliability, safety and complete control of the fuel and oxygen flow, thus thrust. These ‘electric’ rockets are ideally suited for launch vehicles with human occupants.
BENEFITS FOR THE MARINE SECTOR
PWP Hybrid marine generators and drives save both weight and volume which is important when considering new zero-carbon fuels such as hydrogen, ammonia or magnesium hydride that require larger storage volumes than standard marine diesel fuel.
PWP open bore motors can be design around a ducted propeller with omni-directional thrust capabilities. This novel shaft-less design would be a significant space saver in the engine room and also remove the need for a rudder. The open bore motor would be entirely sealed to avoid sea-water contact and corrosion. This alternative design could offer both forward and rear propulsion of a very large vessel, significantly improving slow speed manoeuvrability in harbours and canals.
PWP DC motors and generators produce very low rf-noise, making them suitable for sensitive naval applications. In general, PWP technology is well suited for ships and submarines where both AC & DC power requirements exist as a single shaft rotor can be assembled to generate both current forms. Drive trains comprising prime mover, generator and motor require zero high current electronics, resulting in extremely efficient and versatile drives with complete control over the whole power and speed range, accompanied with high reliability and low to no maintenance.